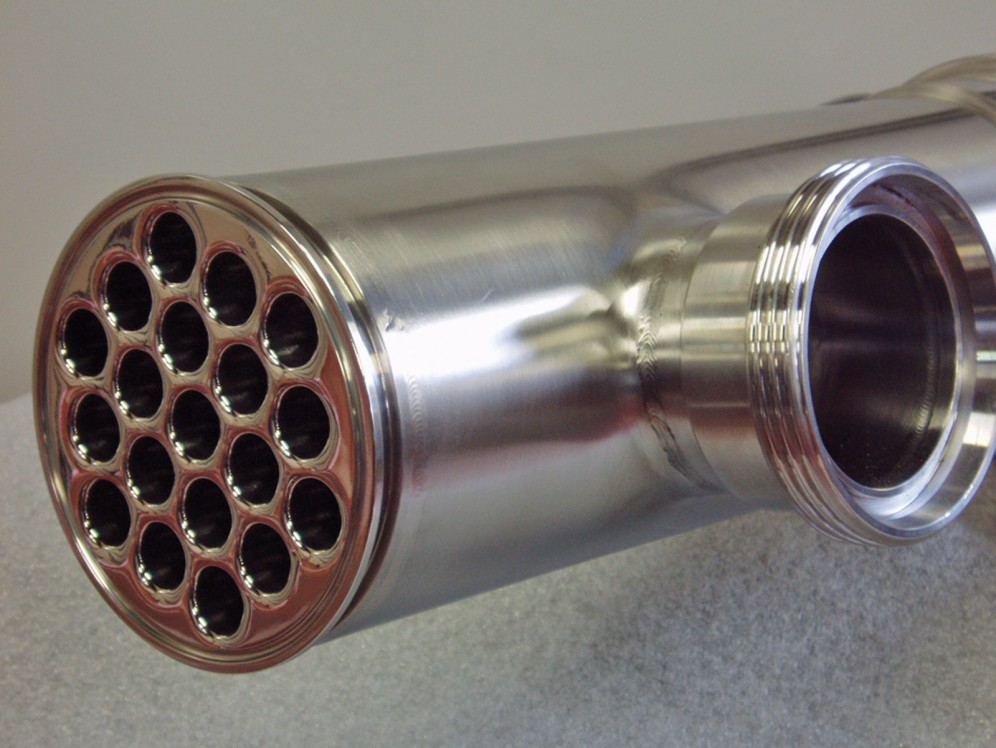
Dove la viscosità o le sospensioni non permettono il trattamento termico a piastre, le aziende ricorrono agli scambiatori di calore tubolari con svariate tipologie di costruzione e di materiali, in base alla resa termica, portata, tipo di prodotto da trattare e ingombri. Gli scambiatori tubolari sono utilizzati in produzioni lattiero-casearie particolari, come i trattamenti di prodotti a media-alta viscosità, con eventuale presenza di particelle, quali ricotta, mascarpone, caseari spalmabili, dessert a base latte, formaggi fusi, frutta per yogurt, topping per gelato ecc. La parete di scambio non è rappresentata dalla piastra ma da un tubo, a sezione cilindrica, di diametro contenuto. Il prodotto scorre all’interno mentre all’esterno passa il fluido di servizio (per il riscaldamento: vapore diretto fino a 150 °C o acqua surriscaldata; per il raffreddamento: acqua di rete, di torre, acqua gelida e, in casi speciali, anche acqua glicolata, freon). Se il trattamento lo richiede, nello scambiatore può esserci un unico flusso di fluido di servizio con più tubi-prodotto.
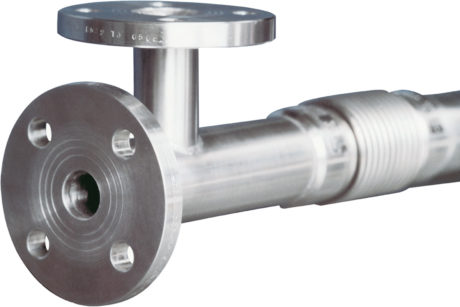
Il tubo è composto da tubi in cui passa il prodotto, posti all’interno di un mantello esterno, in cui transita il fluido di servizio che procede in controcorrente per migliorare l’efficienza dello scambio, scorrendo nel mantello del singolo elemento e passando nel mantello dell’elemento successivo attraverso un’apposita connessione. Gli scambiatori di calore tubolari consentono di lavorare portate industriali di 30.000 l/h e oltre. Le lunghezze maggiormente utilizzate sono di 6 e 3 metri. I tubi a contatto del prodotto prevedono una certa varietà di diametri: 16, 20, 25 mm e oltre. A differenza delle piastre, i tubi non hanno punti di contatto, consentendo il passaggio agevole anche di prodotti con particelle. Gli scambiatori di calore a fascio tubiero hanno autonomie di lavoro maggiori e una manutenzione più semplice e meno costosa di quelli a piastre. Di contro, hanno un’efficienza minore, in particolare nelle funzioni di raffreddamento/refrigerazione, richiedono investimenti e ingombri maggiori.
Per migliorare l’efficienza dello scambio termico, le aziende costruttrici ricorrono alla corrugazione, una particolare lavorazione che viene effettuata sul tubo liscio per ottenere una superficie interna in grado di creare una maggiore turbolenza termofluidodinamica nel moto del fluido. Per effetto della corrugazione il rendimento dello scambio termico viene incrementato in percentuale variabile dal 40% al 90% in funzione dei seguenti parametri: tipo di prodotto, profilo adottato, applicazione. I vantaggi sono molteplici: diminuzione delle superfici necessarie, riduzione dei tempi di contatto e stazionamento del prodotto all’interno dell’elemento, diminuzione dei tempi di lavaggio grazie alla maggiore azione meccanica creata dalla turbolenza, possibilità di lavorare ad alte pressioni e temperature.
Le diverse tipologie
Nella tabella sono descritte le principali tipologie di scambiatori tubolari, escludendo i casi più particolari e meno utilizzati nell’industria lattiero casearia (fonte: Manuale lattiero caseario di Tecniche Nuove). Gli scambiatori monotubo prevedono che il prodotto passi all’interno di un unico tubo, mentre il fluido di servizio scorre nel mantello. Presentano un’efficienza termica limitata, ma sono consigliati in caso di presenza di pezzi. Quelli multitubo sono i più diffusi. Nel caso del multitubo convenzionale, il prodotto scorre all’interno dei diversi tubi, mentre il fluido di servizio scorre nel mantello.
In quelli a recupero termico, invece, il prodotto scorre all’interno dei diversi tubi, mentre nel mantello fluisce il medesimo prodotto al fine di avere un effetto di recupero termico. Gli scambiatori concentrici sono utilizzati per il trattamento di prodotti viscosi in assenza di particelle. In questo caso, il prodotto scorre all’interno dello spazio ricavato da due tubi concentrici. Il fluido di servizio scorre nel mantello esterno e in un ulteriore tubo interno. Con questa soluzione, che aumenta la superficie di contatto del prodotto, viene migliorata l’efficienza dello scambio termico anche in presenza di prodotti viscosi che invece la limitano.
Scambiatori di calore a superficie raschiata
Sono utilizzati quando, a causa della viscosità e densità del prodotto, non è possibile ricorrere agli scambiatori a piastre o tubolari. La parete di scambio è un cilindro, in cui il fluido di servizio scorre all’esterno, mentre il prodotto transita al suo interno quasi sempre in controcorrente rispetto al fluido di servizio, che, a seconda dei casi, può essere di riscaldamento o di raffreddamento. In questi scambiatori, il prodotto tende a rimanere sulla parete di scambio a causa dell’elevata viscosità e dell’eventuale presenza di particelle e pezzi. La denominazione di scambiatore a superficie raschiata è dovuta al fatto che per rimuove in continuo il prodotto, interviene un sistema di raschiamento rotante, azionato da un motore e composto da una serie di lame (o coltelli in materie plastiche atossiche, o acciaio inox) a contatto della parete, che forza il prodotto verso l’interno del cilindro. Oltre a raschiare il prodotto dalla parete e convergerlo al centro del cilindro, le lame incrementano la turbolenza e quindi l’efficienza dello scambio termico e assicurano anche un’uniformità termica al prodotto, essenziale in trattamenti di sanificazione quali quelli di pastorizzazione.
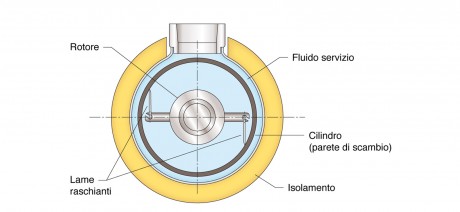
I vantaggi di questo tipo di scambiatore sono di poter trattare prodotti viscosi non trattabili con altre tipologie di scambiatori (a piastre, tubolari) e la possibilità di trattare pezzi. Di contro, richiedono investimenti e costi di manutenzione maggiori (per esempio, il raschiamento della superficie di scambio comporta usure alle lame e anche ai cuscinetti, al cilindro di scambio, al rotore ecc.), costi energetici (fluido di scambio, motori), hanno superfici limitate, con portate industriali contenute, un’efficienza ridotta nelle funzioni di raffreddamento-refrigerazione e possibilità molto scarse di recupero termico. Le case produttrici dispongono di diversi modelli con caratteristiche adattabili alle esigenze specifiche del trattamento termico, quali la superficie in metri quadrati, il diametro dei rotori, la distribuzione delle lame sui rotori (es: sfalsate, due file, 4 file), la morfologia delle lame, il tipo di fluido di servizio e il numero dei giri del rotore.
Stefania Milanello