Non usano il silicio ma la plastica, molto meno costosa e di facile applicazione: sono i sensori del futuro per il monitoraggio degli alimenti freschi negli imballaggi
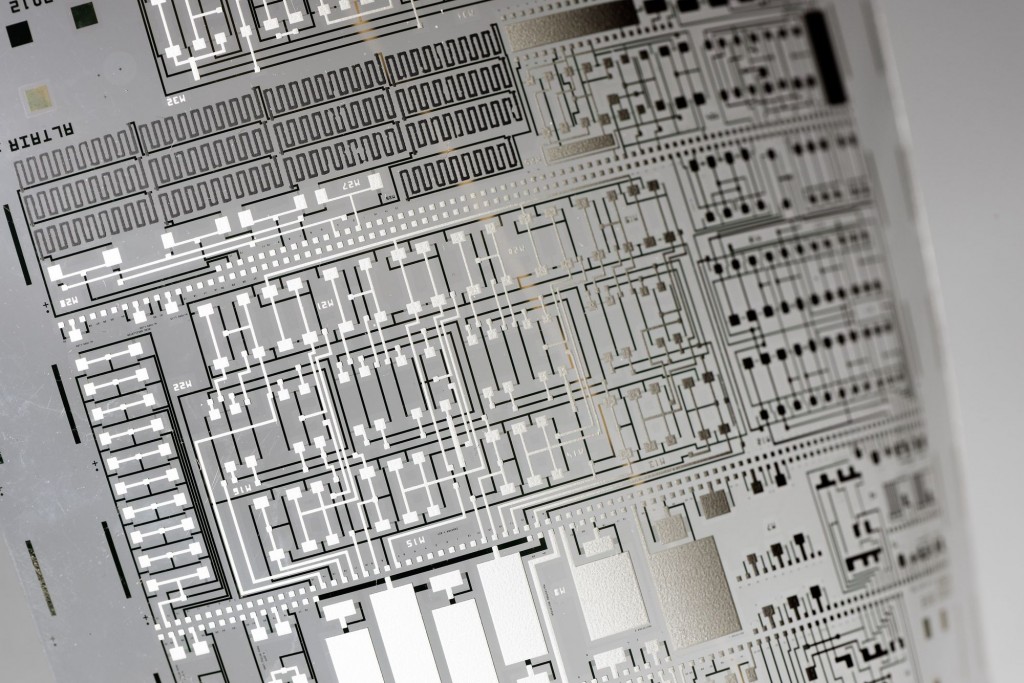
anziché con silicio, per il monitoraggio di alimenti nelle loro confezioni. Economico e veloce da realizzare. © Bart van Overbeeke
Leggere con uno scanner o un telefonino se un alimento è ancora congelato o se per qualche motivo sia stata interrotta la catena del freddo, controllare la temperatura di una confezione di latte o di yogurt e magari anche il suo pH, per escludere alterazioni del contenuto. Sarà presto possibile e senza l’elettronica in silicio. All’Università Tecnica di Eihdhoven (Eindhoven University of Technology), in Olanda, un gruppo multidisciplinare ha infatti sviluppato dei circuiti che possono essere inseriti nei materiali di imballaggio alimentare per monitorare la freschezza dei cibi. La ricerca è frutto della collaborazione dell’ateneo olandese, dell’Università di Catania, del laboratorio francese CEA-Liten di Grenoble e del produttore di semiconduttori STMicroelectronics. La novità sta nei materiali con cui sono realizzati i sensori e l’elettronica di lettura: la plastica anziché il silicio. Perché questa scelta?
Una nuova tecnologia di stampa
Lo abbiamo chiesto a Eugenio Cantatore, professore associato di elettronica all’Università Tecnica di Eindhoven e coordinatore della ricerca, che fa parte del progetto europeo Cosmic: «Abbiamo utilizzato una tecnologia che permette di stampare transistor a effetto di campo usando come semiconduttori materiali organici, quindi a base di carbonio, con costi per unità di area molto inferiori a quelli del silicio. I materiali conduttivi sono delle paste adesive caricate con argento, mentre l’isolante è costituito da un polimero fluorurato».
Il circuito elettronico è realizzato con metodi serigrafici. I transistor hanno dimensioni fino a 5 micron (millesimi di millimetro) e sono piuttosto grandi per la microelettronica. «La lunghezza di canale di un transistor in silicio di ultima generazione è 22 nanometri (milionesimi di millimetro), mentre i nostri dispositivi organici hanno lunghezze nell’ordine dei 5000 nanometri», continua Cantatore. «Questa notevole differenza dimensionale è dovuta al fatto di utilizzare la serigrafia, un metodo di stampa che può essere applicato su grandi superfici in modo veloce: un vantaggio per la produttività industriale e l’economia del processo».
I transistor possono essere stampati sul packaging perché sono portati a bassa temperatura (100-250 °C), anziché alle temperature elevate necessarie quando si lavora il silicio (da 500 a 1100 °C), usando come substrato polimeri termicamente resistenti come il polietilene naftalato (PEN), affine al PET.«Al momento abbiamo sviluppato fogli di elettronica stampata che misurano 11 x 11 cm, ma si sta già lavorando a circuiti in formato A4. L’obiettivo è lavorare su fogli di plastica a basse temperature con materiali organici per ottenere un dispositivo che possa essere fabbricato a basso costo per area, su superfici estese. Il sensore che abbiamo per ora creato può tranquillamente essere inserito in un imballaggio alimentare» fa notare Cantatore.
La lettura dell’informazione
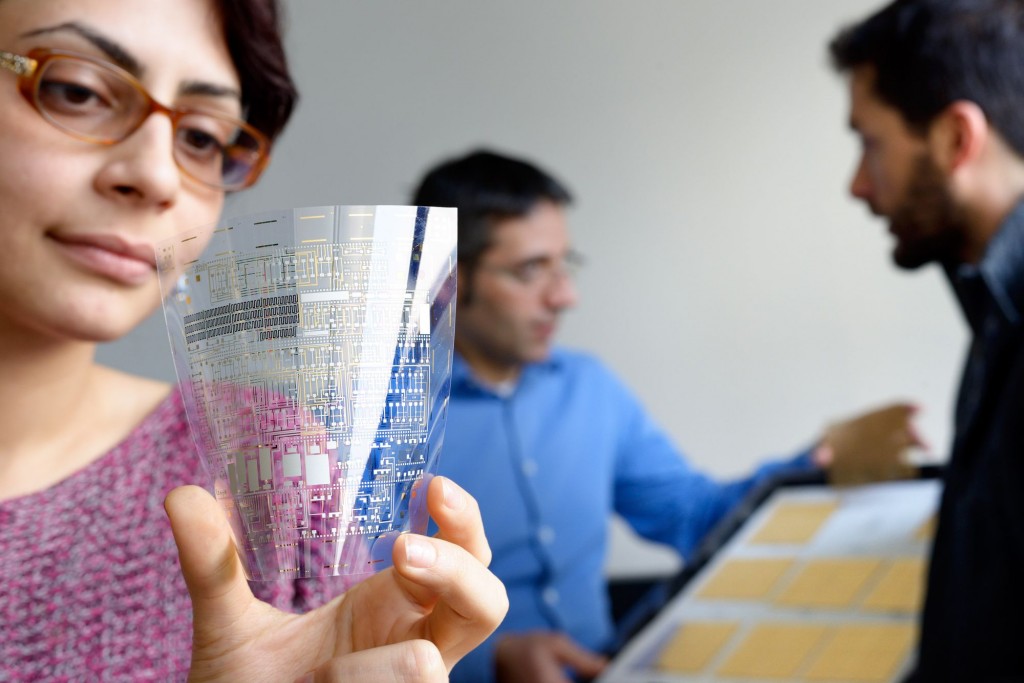
L’informazione è amplificata da un dispositivo che si interfaccia al sensore. Quest’ultimo trasforma l’informazione fisico-chimica, o microbiologica, in un segnale elettrico piccolo che è amplificato e poi convertito in una rappresentazione digitale. «Una parte importante della catena di elaborazione è il convertitore analogico-digitale. Questo circuito preleva una tensione in ingresso analogica (che può avere un valore continuo qualunque tra due valori estremi) e la trasforma in un numero che indica dove si trovi tra un valore “zero” e uno massimo. Per leggere questo valore usiamo una semplice radio, la medesima utilizzata nei badge (RFID), che dobbiamo ancora integrare nel sistema, ma che abbiamo già sperimentato in altre ricerche.
Sia l’invio dell’energia che serve a elaborare il segnale del sensore, sia la lettura del segnale possono pertanto avvenire con onde radio, senza bisogno di contatto diretto», spiega Cantatore. E aggiunge: «Si può pensare di fare dei sistemi per leggere queste informazioni in grandi quantità (es. all’uscita della merce dalla fabbrica) oppure da inserire sotto forma di applicazione negli smartphone al servizio del consumatore per controllare, per esempio, se la qualità del latte che sta acquistando sia ancora buona: basterebbe avvicinare il telefonino alla confezione e leggere le informazioni».
Le applicazioni
I nuovi sensori sono ancora in una fase di ricerca e sviluppo, lontana dall’industrializzazione e dall’applicazione commerciale. «Per ora stiamo lavorando sul monitoraggio della temperatura di conservazione degli alimenti, un’applicazione tecnicamente più praticabile di altre». Ma esistono anche altre possibilità applicative, che richiederanno più tempo per essere sviluppate. «Per esempio, la misura del pH e il suo monitoraggio: c’è bisogno di molta ricerca per individuare un sensore di pH che possa essere affidabile e duraturo anche inserito in un packaging. Siamo inoltre interessati a sviluppare sensori microbiologici, ma non abbiamo ancora avviato le relative ricerche.
Tuttavia, le dimensioni dei nostri transistor sono abbastanza compatibili con quelle dei batteri (attorno al micron) e per questo potrebbero trovare applicazione nello screening microbiologico». Esistono già microchip in silicio per applicazioni biologiche, ma sono generalmente più adatti allo screening di Dna, cioè di molecole biologiche, piuttosto che di microrganismi, poiché questi ultimi sono grandi per un chip in silicio. Inoltre, poiché i nuovi sensori possono essere realizzati su superfici piuttosto estese, possono essere funzionalizzati in molti siti, a vantaggio della sensibilità, che risulta incrementata.
«Mentre con il silicio non si possono realizzare superfici grandi, che costerebbero moltissimo. La prima applicazione a cui abbiamo pensato è il controllo dell’acqua potabile, molto utile in Paesi dove i sistemi di potabilizzazione e distribuzione dell’acqua sono poco affidabili. Ma è probabile che sarà realizzata anche un’applicazione nel settore lattiero-caseario, per esempio per il monitoraggio della carica batterica nel latte», conclude Cantatore.
[box bg=”#cccccc” color=”#000000′ title=”Sensori di plastica: vantaggi in uno sguardo”]- Facili da inserire in packaging anch’essi di plastica;
- Stampabili su ogni genere di superficie flessibile e quindi poco costosi;
- Produzione molto più a basso costo e a risparmio energetico (bassa temperatura) rispetto a soluzioni a base di silicio.