Sollevare i fagotti di cagliata e movimentarli oggi è più facile, meno dispendioso e più sicuro.
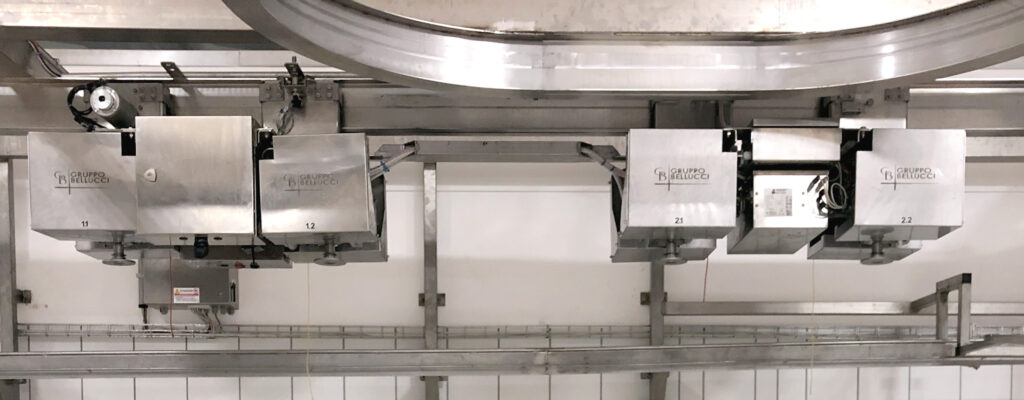
Sollevare le tele cariche di cagliata e movimentarle sono attività molto dispendiose e centrali per sicurezza sul lavoro, miglioramento delle condizioni lavorative ed efficientamento dei costi. La risposta di Tecnomeccanica Bellucci è il PF-W4: un impianto di raccolta e movimentazione automatica dei fagotti composto da almeno due carrelli che operano lungo una monorotaia sopraelevata, dotati di due ganci ciascuno, per gestire due doppifondi simultaneamente. La particolarità dell’impianto sta nell’alimentazione, che avviene con batterie al litio molto performanti, e nel sistema di controllo gestito tramite connessione wi-fi. Ciò permette ai carrelli di muoversi in completa autonomia, senza alcun vincolo dovuto a connessioni cablate e in maggiore sicurezza. Il carrello è versatile nel suo percorso, offrendo la scelta fra un tragitto più breve per giungere allo scarico oppure uno che eviti le caldaie occupate dalla lavorazione, a seconda delle istruzioni impartite dall’operatore.
Carrelli wi-fi
È possibile utilizzare più carrelli operanti in modo indipendente. Ognuno è dotato di un proprio plc collegato via wi-fi con il sistema centrale, il quale coordina i vari spostamenti sulla linea in modo che questi non si incontrino mai e gestiscano nel minor tempo possibile il maggior numero di doppifondi. A corredo, dotazioni di sicurezza e antinfortunistica come sensori di prossimità con segnalatori acustici e led sui carrelli. Strumenti che quando rilevano un ostacolo sul percorso rallentano il carrello o ne interrompono la marcia. L’alimentazione dell’impianto avviene con una linea a 24 V in corrente continua. Questo lo rende molto più sicuro sia durante il periodo di lavoro sia durante le fasi di manutenzione, oltre che efficiente poiché caratterizzato da ridotti consumi di energia. I motori elettrici che sollevano i ganci sono tarati per sollevare il peso dei fagotti, e per bloccarsi se sottoposti a carichi maggiori.
Il sistema di scarico automatico e la movimentazione assistita da un braccio pneumatico per l’inserimento in fascera completano la dotazione dell’impianto di Tecnomeccanica Bellucci. Il PF-W4 è idoneo alle specifiche di industria 4.0 e nelle valutazioni dei PSR è considerato un intervento utile al miglioramento della sicurezza sul lavoro. Inoltre diminuisce i tempi di scarico dei doppifondi e libera spazio a terra facilitando la movimentazione in sala cottura.
Sistema automatico
Una volta attivato, il carrello automatico esce dalla postazione di ricarica e avvia il ciclo di raccolta programmato o, se diverso da quello impostato dall’operatore, si posiziona al di sopra delle prime due caldaie selezionate, fa scendere i cavi per il sollevamento dei fagotti e attende le istruzioni dell’operatore. Un sistema di aggancio rapido permette di inserire l’apposito gancio nel nodo del fagotto, innescare la fune e avviare il prelievo. Seguendo il percorso programmato, visionabile da software in tempo reale (anche da remoto), il carrello trasporta le quattro forme fino alla zona di sgancio dove, senza l’ausilio dell’operatore, queste abbandonano il carrello e si allineano lungo un percorso di raccolta dimensionato sulle esigenze e le metodologie operative del caseificio.
Liberatosi del carico, il carrello automatico si dirige verso la postazione successiva per riprendere il suo ciclo. Il software è in grado di apprendere se alcune caldaie non hanno ricevuto latte e gestisce il carrello affinché queste vengano tralasciate. Il sistema di movimentazione del carrello gestisce diverse velocità, in modo da spostarsi agilmente da e verso i punti di prelievo e di rallentare solo in presenza di ostacoli, punti sensibili, come curve strette, intersezioni di zone di movimentazione o in fase di scarico.
L’impianto può beneficiare di un sistema di interscambio delle rotaie, simile a quello impiegato per i binari dei treni. Tale opzione permette di ridurre notevolmente il numero di carrelli utilizzati e i metri di rotaia da installare nel caseificio. Tale sistema di interscambio ottimizza anche lo spostamento dei carrelli: riduce i percorsi e aumenta le opzioni di spostamento diminuendo il tempo di trasporto. Terminato il ciclo di scarico, il carrello rientra in automatico verso il punto di stazionamento e ricarica, in attesa del ciclo successivo. La dotazione della batteria al litio è tale da impiegare per un intero ciclo di scarico circa un 5% dell’energia a disposizione, garantendo un tempo di esercizio praticamente ininterrotto per tutta la giornata di lavoro, anche in caso di cali delle performance delle batterie.
Tornando al percorso dei fagotti, che erano rimasti appesi e allineati lungo un binario di raccolta, al termine del periodo di sgocciolamento del siero un braccio meccanico li immerge, a uno a uno, in una vasca d’acqua dove vengono girate, sistemate e poi raccolte dall’operatore, coadiuvato da un manipolatore elettronico di ultima generazione che permette di spostare le forme senza sforzi e sistemarle in fascera. Il passaggio in vasca è facoltativo. In alternativa il fagotto può essere inserito direttamente in fascera dal sistema meccanico.
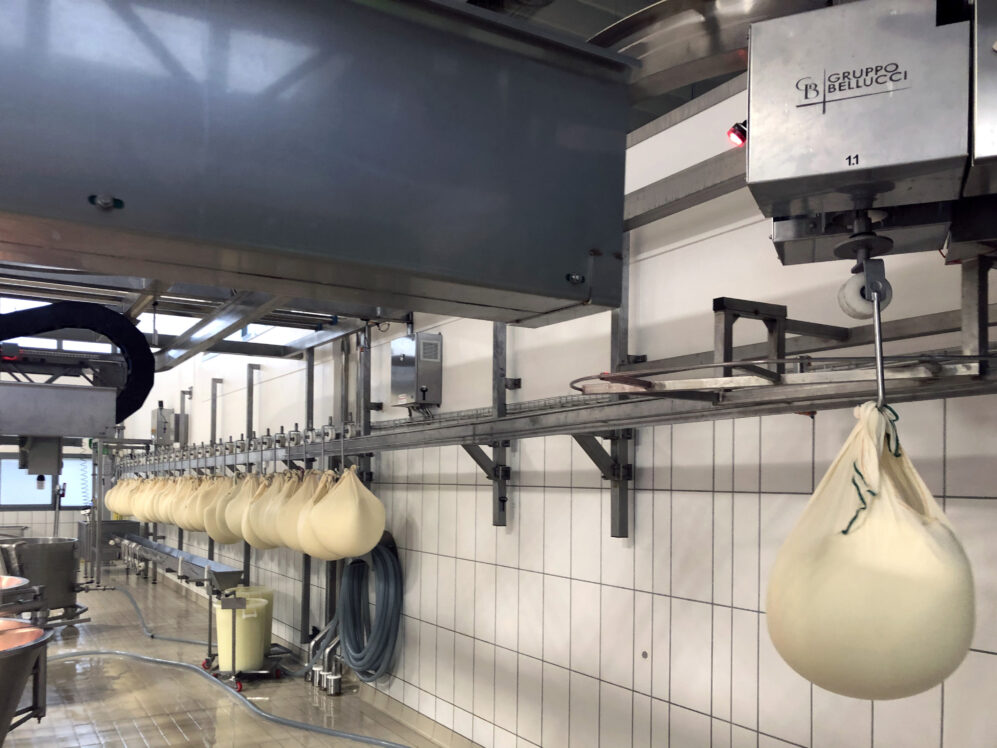
I benefici
Le caratteristiche innovative di cui è dotato PF-W4 “tradotte in pratica e misurate nell’evidenza empirica dei caseifici che utilizzano il nostro impianto”, conclude Massimo Bellucci, titolare di Tecnomeccanica Bellucci, “convogliano verso risultati chiari e abbastanza univoci. Dopo un breve periodo di apprendimento, necessario per adattare l’impianto alle procedure operative del caseificio e istruire gli operatori per utilizzarlo al meglio, i dati raccolti sono encomiabili. Da rilevazioni eseguite da sei mesi a un anno dall’investimento, le tempistiche di scarico dei doppifondi si riducono da un 30% fino a un 60%. Al contempo, il personale coinvolto nelle operazioni di scarico diminuisce da un 20% a un 33% liberando risorse per altre attività a maggior valore aggiunto”.