La separazione mediante filtrazione a membrane nasce nei primi anni ’60 per diventare, circa venti anni dopo, una tecnologia utilizzata anche nell’ambito dell’industria lattiero-casearia per un’ampia serie di applicazioni. Per quanto il principio applicativo sia concettualmente semplice, l’utilizzo della filtrazione a membrane implica aspetti complessi, quali:
- conoscenze tecnologiche inerenti sia il prodotto da sottoporre a trattamento sia le frazioni risultanti dalla separazione;
- soluzioni impiantistiche in grado di conseguire le prestazioni industriali attese.
L’elemento tecnologico fondamentale di questo tipo di separazione è rappresentato dalla membrana ossia da uno strato di materiale semipermeabile (polimerico o ceramico) la cui funzione è filtrare un liquido o anche un prodotto semiviscoso secondo una scala fisica molecolare (fig. 1). A tale scopo la superficie della membrana presenta pori di dimensioni misurabili in micron (millesimo di millimetro) o nanometri (milionesimo di millimetro) (fig. 2). Attuando lo scorrimento di un liquido su membrane con tali porosità e applicando allo stesso un’adeguata pressione si verifica l’attraversamento della membrana da parte di alcuni costituenti del prodotto. Il risultato finale della separazione è in funzione della specificità dei costituenti il prodotto e delle caratteristiche della membrana utilizzata.
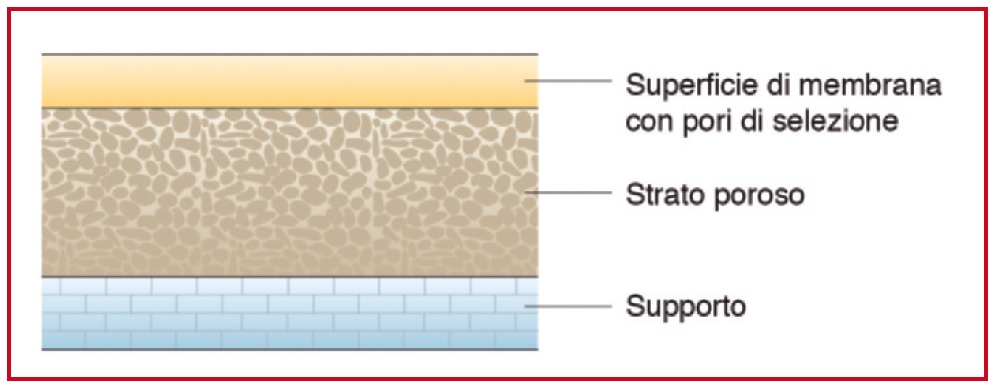
Infatti, la separazione su base dimensionale di tali costituenti permette di ottenere la concentrazione, la chiarificazione, il frazionamento e altro ancora del prodotto sottoposto a filtrazione su membrana. Operando su scala molecolare la principale caratteristica di una membrana è quindi costituita dai pori e dal loro diametro, che concorre a classificare la membrana in termini di molecular weight cut-off (MWCO). Il cut-off rappresenta quindi la caratteristica maggiormente distintiva della membrana, poiché consente di determinare le caratteristiche del permeato e quindi di conseguire i risultati attesi. Per quanto ogni tipologia di membrana sia classificata in base al proprio cut-off, quest’ultimo è fondamentalmente una misura ideale di riferimento, dato che le tecniche di produzione delle membrane non consentono di ottenere per tutti i pori diametri ripetibili e accurati.
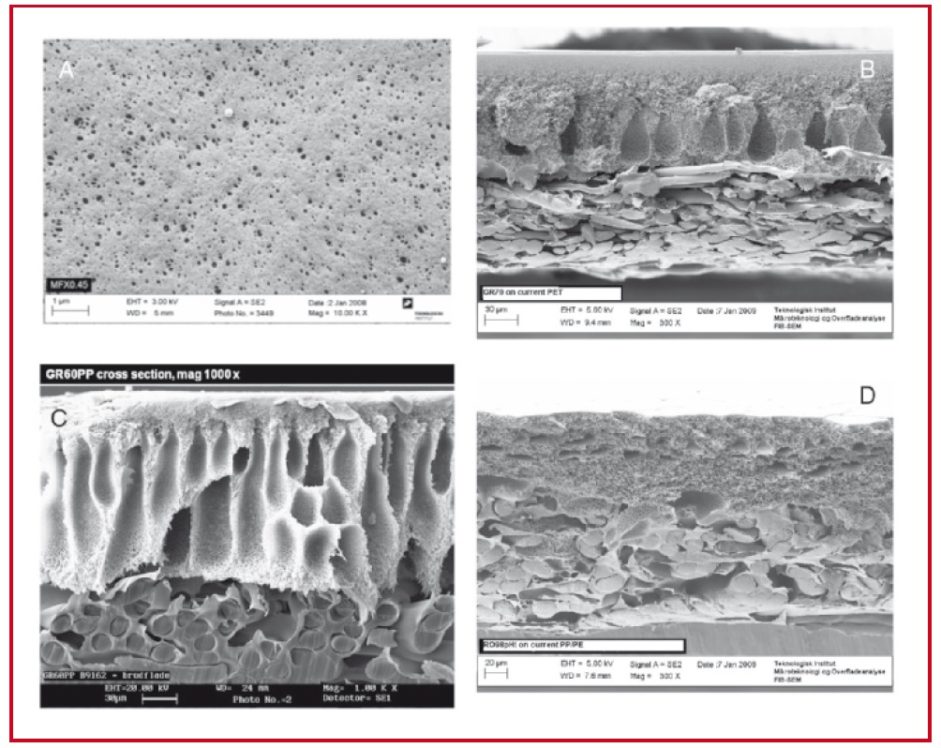
a) membrana di microfiltrazione: superficie con pori di selezione, ingrandita 10.000x;
b) membrana di ultrafiltrazione: sezione laterale della struttura, ingrandita 300 x;
c) membrana di ultrafiltrazione: sezione laterale della struttura, ingrandita 1000 x;
d) membrana di osmosi inversa: sezione laterale della struttura, ingrandita 300x.
Per b), c), d): si noti come la superficie di selezione – molto sottile – sia posta in alto, mentre in posizione intermedia è situato lo strato poroso (attraverso il quale defluisce il liquido separato) e infine in basso si trova il supporto della membrana
Il valore di cut-off è quindi indicativo, in quanto medio, al punto che a parità di cut-off nominale le prestazioni di confronto tra le membrane possono essere differenti (figura 3). Avendo a disposizione nella pratica industriale varie tipologie di membrane, a loro volta contraddistinte da caratteristiche operative precipue (densità e dimensioni dei pori, ecc.), si possono ottenere, a parità di prodotto da trattare, effetti di separazione o frazionamento estremamente diversificati. Quali che siano le membrane utilizzate, un processo di separazione prevede comunque che da un prodotto liquido si ottengano due frazioni: il permeato e il ritentato (o retentato) (fig. 4).
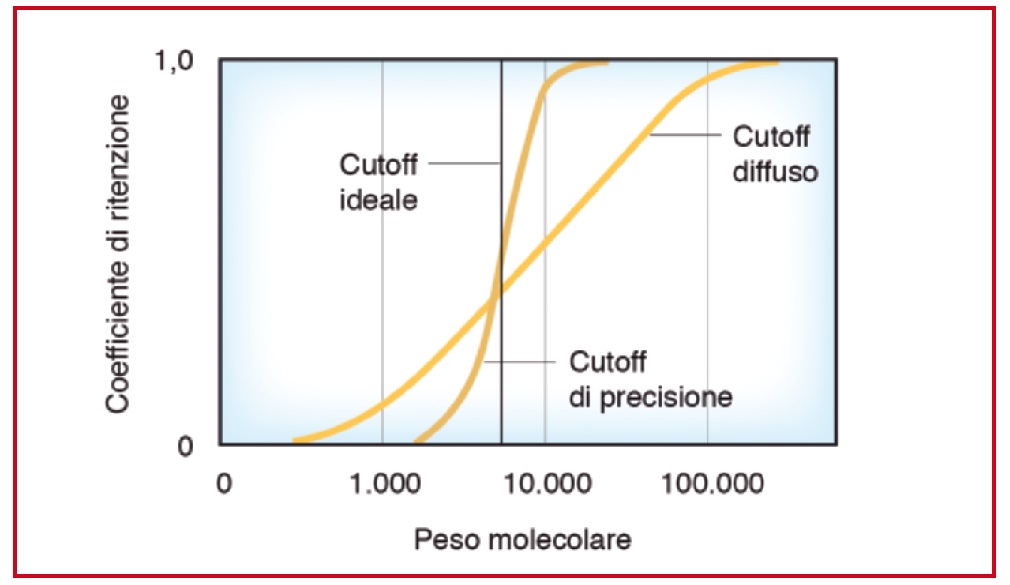
Il permeato è la frazione di prodotto che attraversa la superficie della membrana (per esempio, l’acqua), mentre il ritentato è la frazione residua concentrata costituita da molecole che non permeano la membrana in quanto di dimensioni superiori al diametro dei pori della membrana. Il permeato, il ritentato o entrambi possono costituire il prodotto-obiettivo finale del processo. Per esempio, la rimozione di batteri dal latte, mediante membrane di microfiltrazione, si prefigge come obiettivo il permeato. Se invece si effettua la concentrazione del siero mediante membrane di osmosi inversa, la ragione del processo è il ritentato.
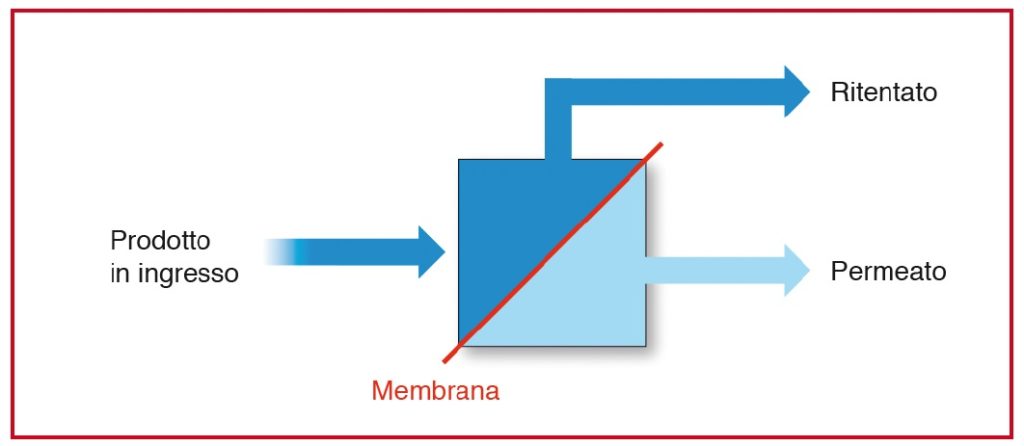
Principio di separazione
La filtrazione membranica opera diversamente dalla filtrazione convenzionale dove l’obiettivo è la separazione dei solidi dal liquido principale. Nella filtrazione convenzionale, il flusso viene indirizzato perpendicolarmente alla superficie filtrante, con un’autonomia di lavoro progressivamente decrescente e solitamente per tempi limitati prima dell’intasamento finale (fig. 5). La separazione a membrane è tangenziale, ossia il prodotto da filtrare scorre parallelamente alla superficie della membrana (fig. 6).
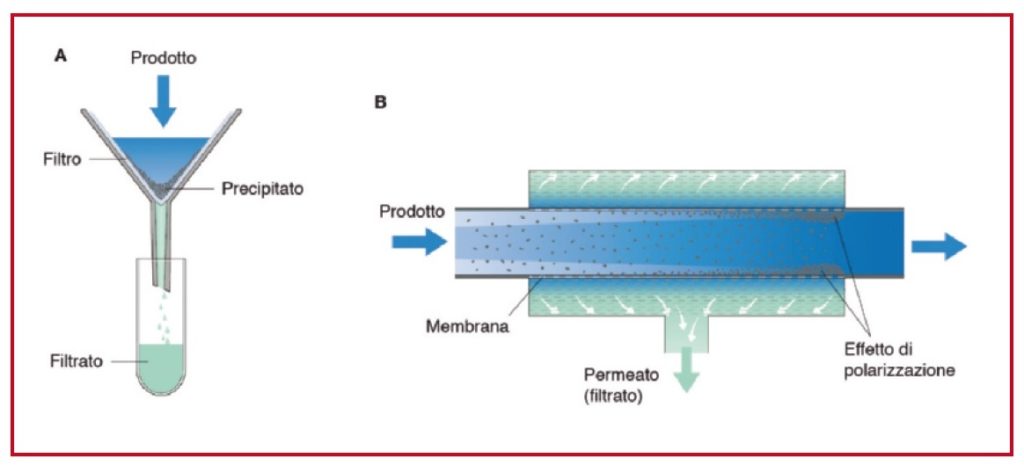
Questa modalità di flusso si propone di conseguire due obiettivi:
- la formazione di uno strato sottile (misurabile in micron) sulla superficie della membrana. È uno strato attivo su cui inizia la separazione, quindi favorisce ulteriormente il processo;
- la prevenzione del fenomeno dello sporcamente progressivo (detto anche polarizzazione) della membrana.
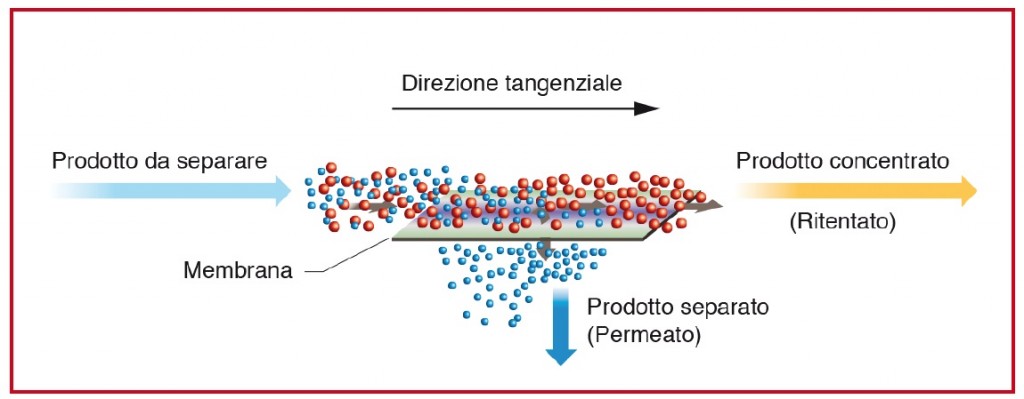
molecolare tra i costituenti sono rappresentate graficamente dalle dimensioni delle sfere
Durante il processo di separazione la membrana è soggetta a sporcamento (polarizzazione), consistente nella formazione di depositi sulla superficie membranica e/o nei pori. A mano a mano che il trattamento procede, la capacità di permeazione tende a diminuire significativamente. È un fenomeno normale, di cui occorre tenere conto nel dimensionamento progettuale delle unità industriali di separazione. Quando la permeazione diminuisce eccessivamente, occorre procedere al lavaggio CIP per ripristinare la capacità filtrante della membrana. Lo scorrimento tangenziale deve evitare l’ispessimento dello strato attivo, in quanto uno sporcamento eccessivo riduce l’autonomia di lavoro, introducendo inoltre un fattore distorsivo della filtrazione vera e propria (come detto lo strato attivo funge a sua volta da membrana addizionale).
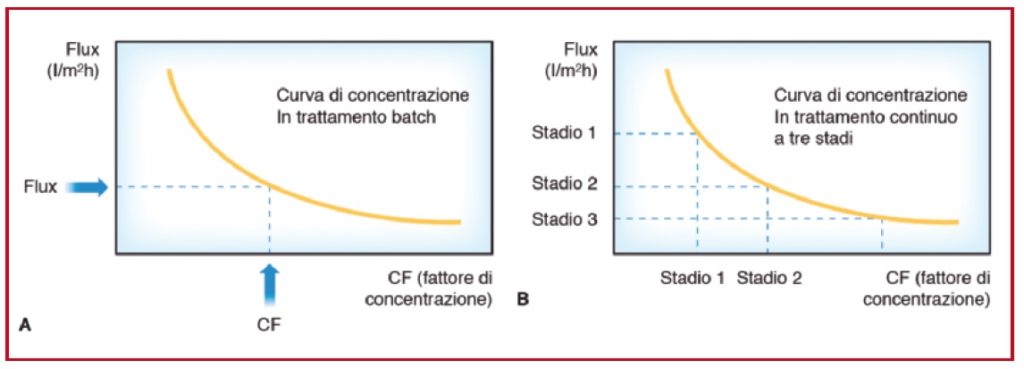
In sintesi, la filtrazione a membrane si realizza con le seguenti modalità:
- il prodotto scorre parallelamente alla superficie (modalità detta di filtrazione tangenziale o cross flow);
- la pressione di scorrimento deve essere adeguata per effettuare la permeazione;
- la velocità di scorrimento deve prevenire rapidi fenomeni di sporcamento della superficie (effetto di polarizzazione: in pratica, i pori si intasano e riducono la portata di attraversamento);
- il cut-off prescelto della membrana deve essere congruo con il risultato di separazione/frazionamento/concentrazione atteso.
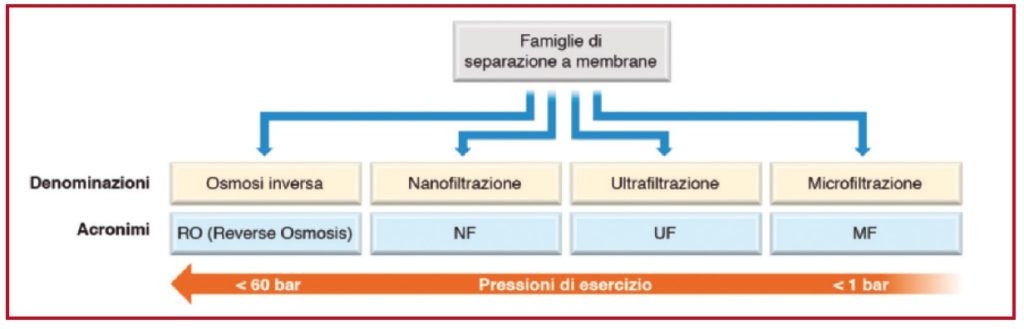
Le membrane si caratterizzano anche per le prestazioni definite dai seguenti parametri:
- capacità di permeazione del prodotto. Si misura in Flux, corrispondente a litri permeati da un metro quadro di superficie in un’ora (l/m2/h). A parità di membrana il valore di Flux è differente per categoria di prodotto, inoltre, uno stesso prodotto può presentare Flux differenti. Solitamente elevato all’inizio della filtrazione, il Flux diminuisce progressivamente come conseguenza dello sporcamento progressivo delle membrane; il valore di Flux è normalmente più elevato alle alte temperature (55 °C);
- fattore di concentrazione, ossia il fattore che esprime il rapporto tra il volume del prodotto in ingresso e il volume del ritentato ottenuto (che quindi risulta essere concentrato x volte) (fig. 7). Viene definito con l’acronimo CF (concentration factor); per esempio, un fattore di concentrazione 10x significa che il volume del ritentato (prodotto- obiettivo) è 1/10 del volume del prodotto in ingresso (ovviamente in questo caso il permeato corrisponde a 9/10 del prodotto trattato). Nelle varie applicazioni di filtrazione a membrana i fattori di concentrazione possono essere molto vari (da 1,2x nella concentrazione di latte per destinazione yogurt a 200x nella separazione di latte magro con microfiltrazione ceramica). Tuttavia, sussiste un fattore limitante rappresentato dai solidi residui finali del ritentato, che in linea di massima si attestano attorno al 20-22% con casi specifici di valori maggiori o minori.
- ritenzione di costituenti. Se un costituente non riesce ad attraversare la membrana e quindi permane nel ritentato, si definisce la sua ritenzione equivalente al 100%. Si ha invece una ritenzione nulla quando il costituente attraversa liberamente la membrana ed è presente nella stessa misura tra permeato e ritentato.
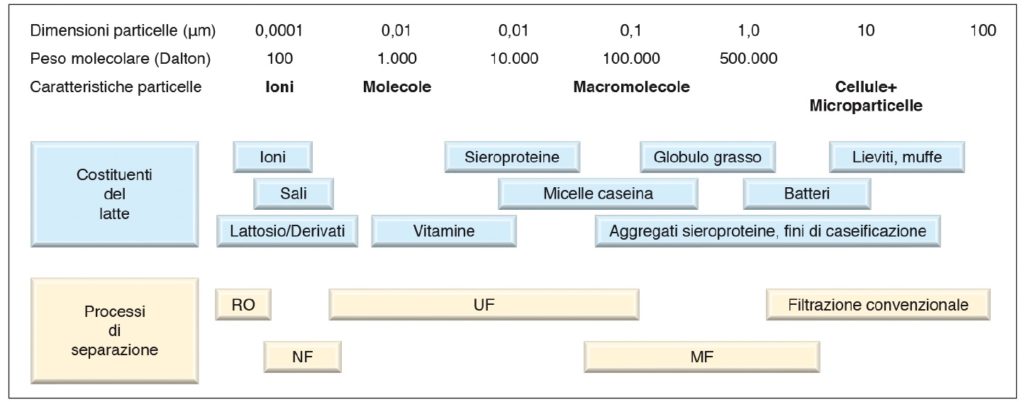
È necessario infine considerare che a causa dello scorrimento sulle superfici e dell’attraversamento di più elementi, la pressione in ingresso diminuisce al momento della fuoriuscita, in quanto subisce delle perdite di carico. Queste ultime sono determinate dalla relazione: P = P1 (ingresso) – P2 (uscita). Più il valore delle perdite di carico P è elevato, più alta è la velocità di passaggio nel modulo e maggiore è lo sforzo di taglio sulla superficie, minore è l’effetto di sporcamento. Naturalmente possono esserci limiti di resistenza meccanica della membrana. Tuttavia, nell’economia di un’applicazione di filtrazione, occorre tenere in debito conto che più la pressione è elevata maggiori sono i consumi energetici delle pompe che provvedono all’alimentazione.
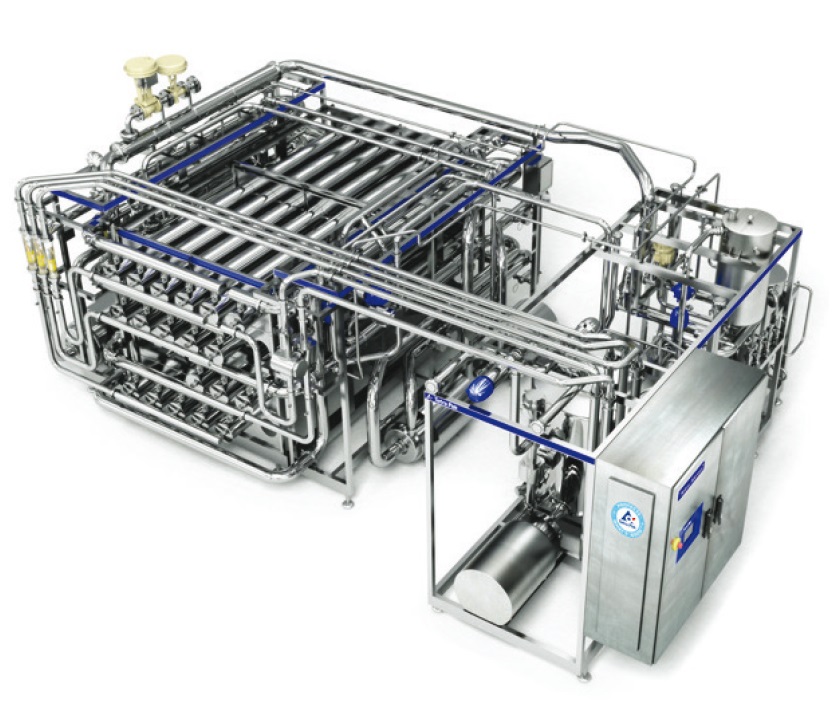
Processi di filtrazione
Esistono quattro tecnologie di separazione a membrana, le cui denominazioni sono oramai divenute di uso comune (fig. 8). Gli effetti della separazione di prodotti lattiero caseari liquidi mediante filtrazione a membrane sono peculiari. Infatti, i liquidi presentano normalmente una composizione complessa, fatta di molteplici costituenti, quali per esempio globuli di grasso, proteine, lattosio, sali minerali, acqua ecc. Non solo, nel liquido possono essere presenti anche spore, batteri e microparticelle. Oltre a un’eventuale dimensione fisica (micron o nanometri), ognuno di questi costituenti o solidi presenti si connota per una propria dimensione molecolare o, più correttamente, per un proprio peso molecolare (espresso con l’unità di misura Dalton) (fig. 9).