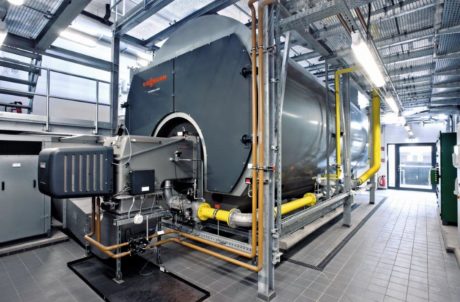
Nella scelta di un generatori di potenza termica destinata alla produzione di vapore occorre considerare diversi aspetti come le performance, il corretto dimensionamento, l’efficienza energetica e la salvaguardia dell’ambiente
Essendo il vapore tra i fluidi di servizio di maggiore impiego in ambito lattiero-caseario occorre rivolgere la giusta attenzione anche ai generatori di potenza termica destinata alla produzione di vapore (saturo), genericamente a “uso tecnologico”.
Nel settore lattiero-italiano sono molto diffuse le caldaie (monoblocco) con producibilità oraria intorno alle 3 t/h. Relativamente alla produzione di vapore, un parametro tecnico determinante è la pressione. Va ricordato come si parli di una pressione: bassa, per valori fino a 1 bar; media, fino a 15 bar, intervallo di valori tipico delle applicazioni in ambito lattiero-caseario; e, infine, di alta quando si superano i 15 bar. È poi fondamentale precisare come si faccia riferimento alla pressione “di esercizio”, da non confondere con la pressione “di bollo”, parametro tecnico massimo che riguarda il dimensionamento strutturale e l’omologazione dei generatori.
Scegliere oculatamente
Una cattiva abitudine che spesso si verifica con i generatori di vapore è la scarsa attenzione rivolta verso questi da parte dei gestori degli impianti, quasi venissero “dimenticati” o trascurati. Per esempio, nei caseifici in cui si lavorano formaggi duri, come il Parmigiano, la caldaia funziona generalmente in modo intenso solo per poche alcune ore durante la mattina. Ma, se è richiesto di ripartire, deve essere in grado di garantire la piena disponibilità. In queste situazioni, la caldaia si trova a essere soggetta a continue e repentine partenze a freddo senza che vi sia un opportuno graduale riscaldamento. Così, il generatore risulta fortemente sollecitato, con possibili conseguenze in termini di integrità delle membrature, e risponde negativamente a livello di efficienza energetica.
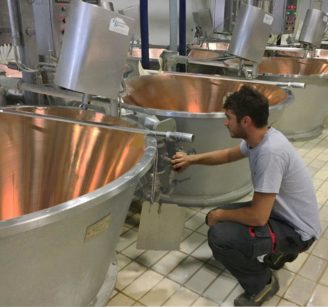
Doveroso, quindi, è sottolineare come solo attraverso un costante monitoraggio e una pianificazione accorta della manutenzione queste macchine possono garantire un’assoluta affidabilità e soddisfare pienamente l’esigenza principe per cui sono stati acquistati!
Manutenzione e assistenza sono condizioni fondamentali per garantire un funzionamento efficiente, così come la scelta del generatore ottimale per le proprie esigenze. Questo viene individuato sulla base della pianificazione e dello sviluppo di un progetto da parte di un progettista, che raccoglie ed elabora tutte le informazioni tecniche, energetiche e logistiche pertinenti allo stabilimento produttivo.
Accade però spesso che nei caseifici e, in particolare, in quelli in cui non si dispone di un progettista, la scelta del generatore da sostituire venga fatta semplicemente leggendo la targhetta della vecchia caldaia, tralasciando tutti gli aspetti di efficienza, rendimento, sostenibilità e tutte le nuove opportunità a livello tecnologico che offre il mercato. La figura del progettista è pertanto importante e diventa necessaria per ottenere buoni risultati e soddisfare le richieste del caseificio. Si eviterebbe, per esempio, di trovare negli stabilimenti lattieri generatori di vapore bollati a 10-12 bar, scelti in maniera non ponderata, basandosi sull’assunto che “sono sempre stati costruiti a questa pressione”. Ciò è tanto più incomprensibile se si considera che la pressione utilizzata nei doppifondi è di circa 2-3 bar (120/130°C) e che pertanto occorre ridurre notevolmente la pressione in uscita dal generatore. In questo modo si abbassa anche il rendimento, ma con l’aggravio di far funzionare il generatore stesso sempre ad alta temperatura. Una scelta economicamente e funzionalmente intelligente potrebbe essere rappresentata da una caldaia con una pressione di bollo inferiore per esempio a 6 bar, per evitare di incorrere in quanto sopra descritto. Non da ultimo, il progettista potrebbe anche valutare e aprire alla possibilità di ottenere certificati bianchi grazie all’efficientamento, quindi alla fine consentire un ulteriore risparmio economico. Questa precisazione permette di considerare più chiaramente un contesto impiantistico generale nel quale di solito operano ditte altamente specializzate in impiantistica con fluidi ad alta temperatura e pressione, oppure grossi installatori che si avvalgono di manodopera specializzata (come i saldatori patentati).
La tecnica costruttiva dei generatori: cenni storici
I generatori di vapore funzionanti a carbone trovarono le prime applicazioni su carri motrici ferroviari (locomotori) e nei caseifici in cui si produceva formaggio in caldaie di rame (doppi fondi). Tali caldaie appartengono alla tipologia costruttiva a tubi da fumo, che possono essere a due giri di fumo (o a fiamma rovescia), ormai datata, o a tre giri di fumo effettivi.
La versione a “tre giri di fumo” consente di ottenere emissioni più basse allo scarico ed è la scelta obbligatoria per poter rientrare nei limiti imposti dalla legge per le emissioni di CO e NOx. Per esempio, per il parametro NOx si va verso la conferma della richiesta di 80 mg/Nm3 per la combustione con metano (in alcune Regioni anche meno). Questa tipologia di caldaia, inoltre, trova sempre maggiore applicazione anche per le piccole potenze. Benefici si constatano anche sul fronte del rendimento “stagionale”, che considera le perdite per stand-by, ovvero quelle causate dalle pause del bruciatore, oppure legate alle perdite per irraggiamento. Per quanto riguarda, invece, la soluzione a “inversione fiamma”, seppur più economica, è sempre maggiore la tendenza a non considerarla.
Il recupero energetico
Fondamentale è sapere che le alte temperature di esercizio comportano perdite non trascurabili di energia termica nei fumi di combustione.
In passato ciò non era assolutamente considerato, così come il recupero di energia (quindi risparmio), perché l’energia aveva costi irrisori rispetto a oggi e altre erano le caratteristiche che venivano tenute in considerazione (per esempio, continuità e semplicità di esercizio). Oggi tutto questo risulta, invece, determinante al fine di raggiungere i più alti gradi di efficienza, Per esempio, l’installazione sull’impianto di scarico di adeguati dispositivi, denominati recuperatori o economizzatori, consente di recuperare parte dell’energia termica dispersa, elevando il rendimento globale dell’impianto, così da garantire migliori prestazioni e un impianto più conveniente dal punto di vista economico. La presenza di apparecchiature di recupero si fa maggiormente pressante in generatori che non presentino elevati rendimenti di partenza.
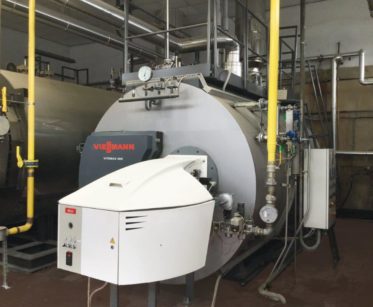