Seppur caratterizzato da esigua marginalità, il settore del latte UHT ha un’arma in più per competere sul mercato: la sterilizzazione in un unico passaggio.
Tecnologie consolidate e mature per un prodotto consolidato, forse un po’ snobbato, approcciato frequentemente come un ripiego. Se questa era l’istantanea dell’industria del latte UHT ora la tecnologia ha aperto una nuova prospettiva. La chiave di volta è stata la semplificazione del processo o meglio il superamento della fase di pastorizzazione. Così ora è disponibile un trattamento termico a partire da latte crudo con produzione immediata del latte UHT e un’adduzione in linea al confezionamento asettico. In pratica, la soluzione “OneStep” – questo il nome della famiglia di soluzioni tecniche scelto dal costruttore Tetra Pak Processing – integra la funzione di titolazione (effettuata da una scrematrice e da un sistema di titolazione del grasso) in una unità UHT. Nella realtà questa integrazione ha comportato un lungo e complesso lavoro di ricerca e di individuazione di soluzioni tecniche idonee.
Titolazione del grasso in un ambito UHT: problema risolto
Nel contesto di una tecnologia UHT convenzionale, la funzione di titolazione è effettuata durante la pastorizzazione. La scrematrice separa il latte dalla panna e pulisce il latte crudo, mentre il sistema di titolazione provvede a titolare correttamente il latte e la panna di risulta. La dislocazione delle due apparecchiature in un processo UHT pone problemi tecnici peculiari. Una scrematrice elimina i sedimenti separati dalla forza centrifuga mediante “scarichi automatici” (detti anche “spari”). Il momento dello scarico produce l’effetto di destabilizzare per un istante l’operazione di scambio termico in corso, che in un’unità UHT può facilmente comportare un’istantanea “perdita di sterilità”. Se tale evento si verifica, la sessione di produzione può ritenersi conclusa anzitempo, con l’inconveniente di dover ricorre a lavaggio CIP e alla presterilizzazione con acqua per poter riprendere la produzione. Pertanto gli scarichi della scrematrice sono fasi di processo che richiedono una soluzione. Anche la titolazione comporta una soluzione speciale, in quanto si rende necessario un elevato grado di precisione in linea. In concomitanza con gli scarichi della scrematrice, la precisione di titolazione è parzialmente compromessa. Nella tecnologia “OneStep” il latte titolato procede direttamente al confezionamento e quindi il titolo deve essere praticamente già conforme. Per assicurare la prestazione si utilizza un sistema di standardizzazione in linea dotato di funzionalità avanzate, quali il governo diretto dello scarico della scrematrice, la partecipazione a momenti tipo svuotamenti-riempimenti di impianto, ri-circolazione acqua sterile ecc. Superata la precisione di titolazione, la gestione dello scarico della scrematrice agli effetti della continuità di trattamento UHT ha richiesto la progettazione di un apposito gruppo di “separazione OneStep” frapposto fra la scrematrice- sistema di titolazione e la sezione di scambio adibita al trattamento finale. Al momento dello scarico della scrematrice il gruppo interviene creando condizioni di assoluta stabilità nelle sezioni di riscaldamento. Inoltre, l’esigenza di alimentare la scrematura alla temperatura ottimale (50-55°C) ha portato a rivedere la configurazione dello scambiatore di calore, suddividendo lo stesso fra area termica a servizio della scrematura-titolazione e area termica a servizio del trattamento finale UHT (comprensiva anche della fase di omogeneizzazione). Fra queste due aree è appositamente situato il gruppo di “separazione OneStep”. Infine, per garantire una stabilità di portata verso il parco confezionatrici asettiche – che per loro natura presentano momenti di interruzione del confezionamento – è stato previsto almeno un polmone asettico. Per una maggior produttività, tuttavia, sarebbe meglio prevederne un altro, in modo da produrre latti a titoli diversi. Lo sviluppo tecnico- tecnologico ha portato a soluzioni che possono operare dalle 20 alle 40 ore consecutive, di tipo sia diretto (a iniezione di vapore) sia indiretto (con scambiatori tubolari).
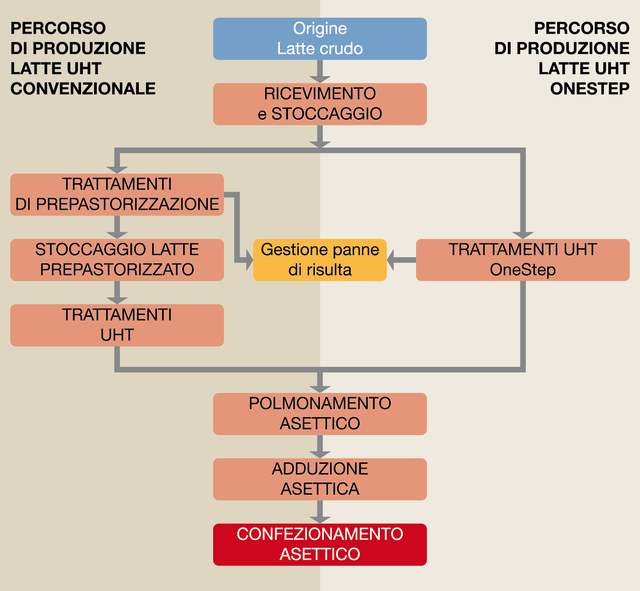
I vantaggi della nuova tecnologia
Riduzione dei costi energetici
Senza la fase di pastorizzazione e di refrigerazione dello stoccaggio latte titolato, la riduzione dei costi energetici e dei servizi (elettricità, vapore, acque, acque di raffreddamento) è attorno al 50%.
Calo delle perdite di produzione
Con la diminuzione dei volumi morti di impianto, le minori perdite di produzione latte – a seguito di minori operazioni di svuotamento-riempimento – sono stimate nell’ordine del 30%.
Semplificazione impiantistica; riduzione esigenze di lavaggio CIP; precisione nella tracciabilità
Con la semplificazione dell’infrastruttura produttiva, i benefici riguardano l’utilizzo delle risorse umane, la riduzione delle attività manutentive e dei lavaggi CIP (dovuta al minor numero di unità di processo), il monitoraggio di tracciabilità meno complesso (quindi più accurato).
Contrazione dei tempi produttivi; miglioramento della qualità di prodotto; incremento di produttività
Dalla tipica durata di due giorni del processo convenzionale (fra l’ingresso del latte crudo in stabilimento e il confezionamento asettico), la tecnologia “OneStep” si può concludere in alcune ore.
Maggior tutela ambientale
Le minori perdite di prodotto si riflettono sui costi di depurazione, con riduzione dei valori di COD anche sino al 40%. Si stima inoltre che i minori consumi (energie, servizi, acque), consentano una riduzione delle emissioni di CO2 nell’ordine del 30-40%.
(Si ringrazia Giuseppe Arienti per la collaborazione)
Elena Rossi