Le centrifughe moderne forniscono maggiore efficienza operativa e minore impatto ambientale consentendo di ridurre i costi e soddisfacendo le sempre crescenti esigenze ambientali in linea con le direttive europee.
Sempre più efficienti e flessibili, le nuove centrifughe strizzano l’occhio all’ambiente. Si tratta di separatori centrifughi ad azionamento diretto del tamburo, con dispositivi di tenuta che assicurano l’ermeticità rispetto all’aria. Il tradizionale tamburo rotante semiaperto con alimentazione dall’alto viene sostituito da un tamburo rotante ermetico alimentato dal basso. Il risparmio energetico che ne deriva rende queste nuove centrifughe perfettamente in linea con le ultime disposizioni normative europee, che incentivano, da parte delle aziende, l’adozione di macchinari a basso consumo energetico. L’utilizzo delle centrifughe di ultima generazione nel settore lattiero-caseario è quello previsto per le tradizionali centrifughe, ovvero: scrematura di latte caldo, latte freddo e siero di latte, pulizia (eliminazione di sedimenti e altre particelle), desporificazione, concentrazione di panne.
Efficienza operativa e risparmio energetico
L’utilizzo di una serie di innovazioni tecnologiche fa sì che il risparmio di energia di tutto il sistema di separazione arrivi anche al 35% rispetto ai separatori centrifughi tradizionali a trasmissione indiretta. Una delle innovazioni introdotte è il motore assiale rispetto al tamburo, con l’adozione di motori ibridi a magnete permanente. Tali motori a trasmissione diretta riducono il numero di parti esposte a usura, migliorando l’efficienza operativa e riducendo i costi di manutenzione e di servizio. Le perdite di energia inferiori migliorano ulteriormente l’efficienza energetica, mentre la minore generazione di calore riduce i costi energetici per il raffreddamento e la lubrificazione delle parti interessate (si arriva a una riduzione del lubrificante anche del 90%). È comunemente noto che le maggiori perdite di energia in applicazioni ad alta velocità di rotazione sono dovute all’attrito. Oltre a un calo dei consumi energetici globali e, pertanto, dell’impatto ambientale, la riduzione dello stesso all’interno del separatore porta alla diminuzione delle temperature delle superfici di contatto prodotto della macchina, con conseguente miglioramento dell’igiene e della pulibilità. Allo stesso tempo l’ambiente di lavoro degli operatori risulta migliorato grazie agli elevati livelli di sicurezza e alla rumorosità ridotta anche di 6 dB (decibel). L’unità di azionamento diretto ha tra le sue più importanti novità la semplicità meccanica. Grazie ad un minimo di parti in movimento è migliorata l’affidabilità meccanica, abbassati i costi di manutenzione e i tempi di inattività per manutenzione, aumentato l’intervallo di tempo fra interventi di manutenzione da 8.000 a 16.000 ore. Non è necessaria alcuna regolazione o sostituzione delle cinghie e i cuscinetti sono esposti a molto meno stress rispetto a quelli in macchine con trasmissione con cinghia. Un minor numero di parti in movimento si traduce anche in meno energia dissipata, meno calore generato e minore energia necessaria al raffreddamento.
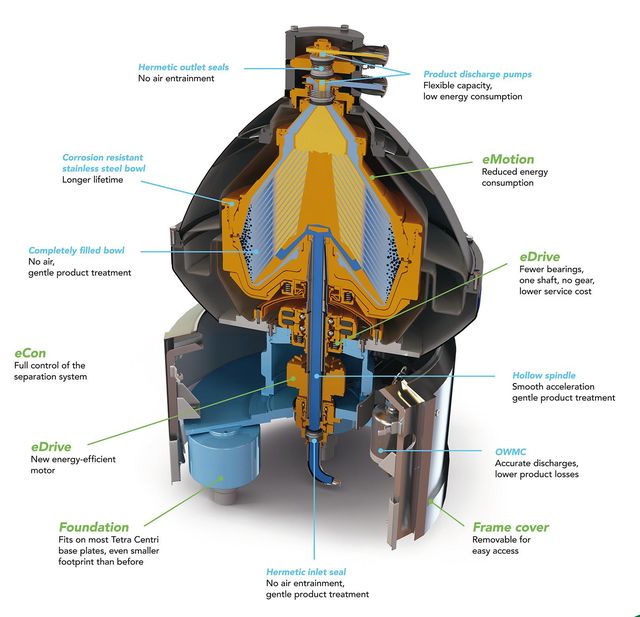
I moderni separatori centrifughi garantiscono anche una maggiore flessibilità operativa, gestendo variabilità di portate di prodotto e di ricetta senza modificazioni meccaniche, grazie anche a efficienti pompe di scarico dei prodotti e a rpm (rotazioni per minuto) variabili. Nelle centrifughe ad azionamento diretto con tenute ermetiche il prodotto da trattare è immesso nel tamburo dal basso. Questo, insieme a un’accelerazione uniforme, consente il trattamento delicato del prodotto, che mantiene intatte le dimensioni dei globuli di grasso. Inoltre, le tenute ermetiche del tamburo rotante all’ingresso e all’uscita del separatore impediscono il contatto del prodotto con l’aria, preservandolo dai danni dovuti all’ossidazione di alcuni suoi componenti. Altra novità riguarda il miglioramento del comando del separatore, con l’utilizzo di interfacce uomo-macchina HMI (in inglese: Human-Machine Interface) che governano tutte le funzioni di gestione in modo da garantire una maggiore facilità di utilizzo, la riduzione al minimo delle fermate non programmate, la disponibilità continua di reportistica di stato della macchina. I nuovi sistemi di controllo integrati consentono all’operatore di visualizzare, in ogni momento, le informazioni significative ed eseguire azioni di controllo e correzione. Tutte le funzioni del sistema sono controllabili dall’operatore o da un sistema di controllo centrale. Il sistema segnala i parametri essenziali che stanno superando livelli critici così da intervenire. I dati possono essere scaricati, salvati e trasmessi a distanza, conservando i report storici per il tempo necessario.
Luca Ornati